
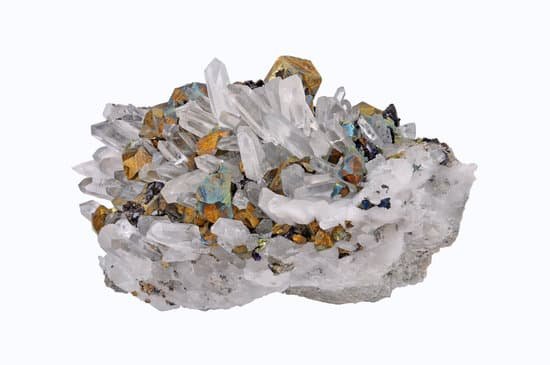
All text should also be recessed, using clear and concise fonts like Arial, Sans-Serif, Verdana, etc. First off, the text inserted into the CAD model should have at least 0.5mm of spacing between each individual character. How to Integrate Text- Do you plan on inscribing a part number, description, or a logo into your part? There’s a few tips you should be aware of when creating a design with text. When integrating threads into the model, keep the size at least above M2, preferably around the M6 mark or higher for the best results. For holes that require tight tolerances, reamers and boring tools can be used. Last but not least, creating holes in you CAD drawing will also call for some careful planning, particularly with the diameter and depth capabilities of the standard drill bit size. If you plan on using plastic material, keep the thickness at 1.5mm or higher.

For designs that you intend to machine out of metal, keep the wall thickness around 0.8 mm or higher. You should also be cautious when decreasing the wall thickness of your model, as this can reduce the stiffness of a material, creating vibrations and lowering the overall surface finish quality. On the other hand, if your 3D model features internal corners that are at a 90 degree angle, add a T-bone undercut into the design. If you’re hoping to achieve a high quality surface finish, you can increase the corner radii above the recommended value by about 1mm. If you have internal edges and corners in your design, the diameter of the cutting tool will also have to be taken into account. By limiting the depth of the cavity to four times the diameter of the tool, you can achieve first-rate results.

For the most part, end mill tools are limited in cutting length, only capable of cutting three to four times their diameter. When designing a model for CNC milling, you’ll always want to be weary of the depth and diameter of any cavities. Therefore, it’s critical that the intricate sections of your CAD model are fully optimized for production. Properly Implementing Cavities, Edges, Walls, and Holes- As versatile as a CNC machine might be, every manufacturing tool has its limitations. Here are some tips to keep in mind when preparing a design for CNC milling. There are a plethora of ways to optimize your design to prepare it for manufacturing, and these factors will oftentimes determine how successful the outcome will be.
IRON CAD HOW TO CHANGE THICKNESS SOFTWARE
Although most CAM software programs will handle the preparation for you, you’ll still have to input certain settings and double-check various aspects of the model before exporting it to DXF. Sounds easy enough, right? Well, there are still other crucial factors to keep in mind when preparing a CAD drawing for CNC milling. From here, simply import the vector DXF file into a CAM/CNC program to generate the necessary G-code.
IRON CAD HOW TO CHANGE THICKNESS PDF
This includes scanning your sketch, saving it as a PDF file, and converting the image into a DXF file. To do this, you’ll trace around the silhouette and the main features of the image, which can then be saved as a DXF file and imported it into a CAM program.Īnother method you can use is automatic image conversion. For instance, you can take an image and manually trace it using vector cut paths. There are a couple of techniques to use when designing models for CNC milling. From here, the drawing will be imported into CAM/CNC software, where it will be transformed into G-code, the programming language that controls and directs the CNC milling machine. Once the design is completed, you’ll have to convert the image into either the DXF or DWG file format. In most cases, the first step of the CNC milling process starts with CAD software, which is where you will create the model you wish to produce. There are a number of steps you should take when designing an object for CNC milling, here are some of the most important things you need to know. Compared to traditional manufacturing techniques, CNC milling offers advantages such as high production speed, greater precision, and automated part cooling.īut before a designer can bring their design to life on a CNC machine, the model must first be sketched on CAD/CAM software. The technology utilizes a rotating cylindrical cutting tool to cut or drill a design from metal or plastic material. CNC milling is one of the most popular options for manufacturing prototypes and parts that entail cutting or drilling.
